Steel Pipe Galvanizing Line
galvanizing pipe line
galvanizing pipe line
Custom Design
We supply custom design for your request. Online machine with your pipe mill.
High Speed and Automatic control
Coating and marking with automatic control
Recycled and Reused Paint
The paint utilization rate is greater than 98%, and the paint can be recycled and reused
Service
All lift service
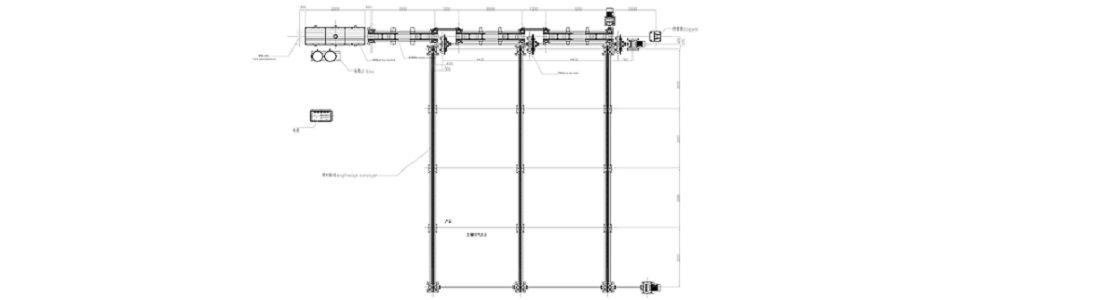