API ERW Tube Mill
ERW pipe mill is a set of high-performance units developed by our company based on the absorption of advanced technology at home and abroad, combined with years of experience of our company. The production line is equipped with comprehensive quality testing equipment according to API standards, which can produce natural gas pipelines and oil pipelines meeting API standards. The annual production capacity of the line is 150,000 tons.
1). Rough forming machine without roll changing
The unit adopts the world's most advanced forming machine, the rough forming machine does not need to change the roll. In this way, roll changing time is reduced and production efficiency is improved, which makes the production of multi-specification and small-batch orders possible.
2). Fast changing roll of fine forming machine and sizing machine
The fine forming machine and the sizing machine adopt roll quick change technology. When changing rolls, the roll changing mechanism pulls out the roll shaft system from the side as a whole, and then sends the spare shaft system to the stand. In this way, roll changing time is reduced and production efficiency is improved, which makes the production of multi-specification and small-batch orders possible.
3). PC control to change specifications
Previous technology, when changing specifications of the roll adjustment, require highly skilled adjustment workers to do so. Due to the uncontrollable human factors, the unit's reject rate is relatively high and the adjustment time is relatively long, which seriously affects the unit yield and production efficiency. Our unit, the establishment of a comprehensive database, changing specifications, only need to input parameters such as diameter, wall thickness, the computer is called roll to adjust the location data of database, the computer will drive roll automatically stop after arrived in correct position, directly into the belt will be able to production, reduce the adjustment time and errors, reduce the rejection rate when the leader.Such adjustment technology, combined with the machine that does not need to replace the roll and the sizing machine that rapidly changes the roll, the unit can change the specification within 2 hours, in the world leading position.
4). Advanced preparation area technology
The unit adopts semi-automatic shear welding machine and automatic unattended accumulator, which realizes that only one worker is needed to operate the material preparation area of the unit and reduces the labor cost.
5). Advanced welds heat treatment technology
The unit adopts advanced NQT weld heat treatment technology. The weld is firstly heated at medium frequency, then quenched, and then the weld is heated again, and then the weld is annealed through a length of air-cooling section. Such a weld heat treatment process can ensure that the test indexes of the weld meet the API-5L standard.
6). Advanced hydrostatic testing technology
The unit adopts advanced high-pressure hydraulic testing machine. The hydraulic press adopts large gap sealing. The boosting cylinder is supercharged to complete supercharging. The pressurized water filling tank is filled with water quickly. Perfect safety measures and comprehensive monitoring system ensure safe and fast running. Fully automatic working mode.
7). Advanced end chamfering technology
The unit adopts advanced end facing machine, and the end facing machine adopts patented fixture to ensure uniform and blunt edge after chamfering of the pipe end, in line with API-5L standard. Three knives are mounted on the cutter head, one flat head, one chamfered edge, one inner burr is removed, and the end face of the tube is clean and clean.
8). Advanced pipe logistics management technology
The unit uses a steel pipe numbering and identification system, so that all steel pipes in the entire production line are in an identifiable and manageable state. The steel pipe will establish communication with each equipment in the finishing area and summarize the steel pipe condition to the control center. When each shift is off work, a production status table is automatically generated, which records in detail how many steel pipes are produced in this shift, how many finished products, how many waste products, and which process the waste products are produced. In this way, the manager can clearly understand the condition of the unit and the production status, and can solve the problem according to the process of waste production.
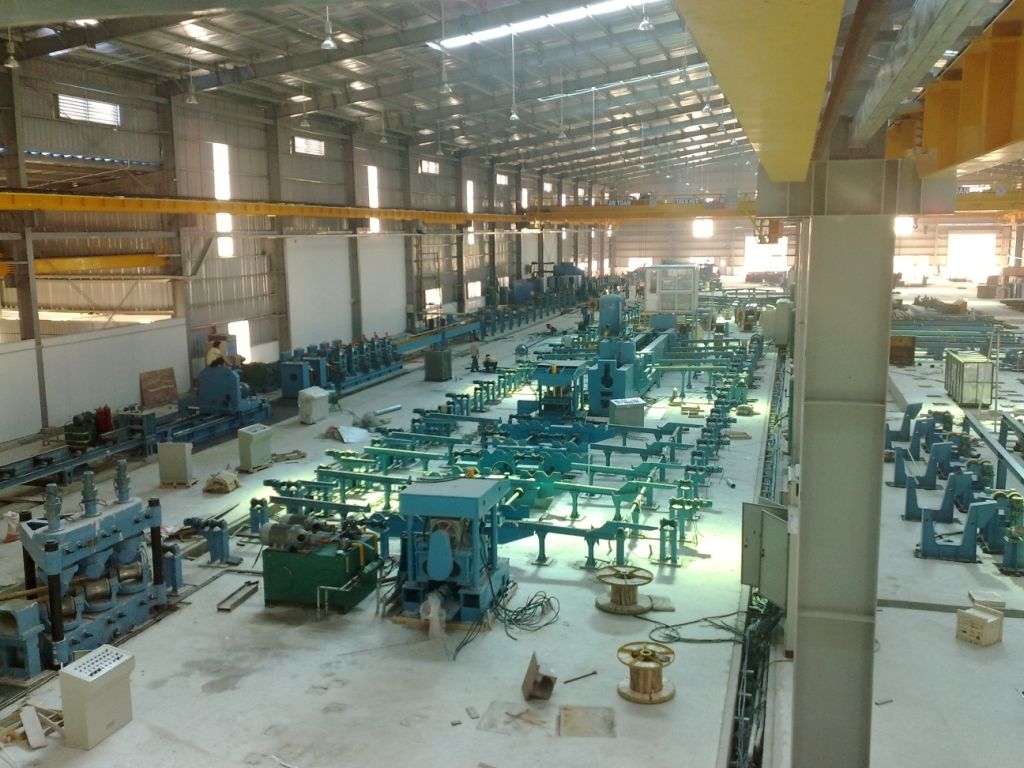
API Tube Mill
API Tube Mill
Custom Design
We supply custom design for your request.
High Precision
High Precision of the Pipe diameter
High Speed
Max can reach 150m/min
Service
All lift service